How is leather made?
Leather is a fine and adaptable material that results from a complex and meticulous process that requires accuracy and attention to ensure a consistent and high-quality product.
The process begins with a skin from an animal and near the end of the process there’ll be a leather piece ready to be made into clothing, a bag, or any leather product.
How Leather Is Made
Here is the process of making leather:
Raw Materials
The first step is to obtain the skin from the animal, which can be a pig, a sheep, a goat, or a crocodile, but most often it is a cow. The skins are waste products of the dairy and meat industries and are a valuable resource that can be turned into leather for making clothes, bags, and other items.
The quality of the skin depends on how the animal was raised, which can affect how much leather can be produced from it.
For instance, if the cow has suffered from branding, insect bites, barbed wire cuts, or electric shocks, the skin may have scars or holes that lower the yield to around 60%. The diet of the animal can also influence the quality of the skin.
The skin is removed quickly to prevent moisture loss, and the focus is on clean and unblemished surfaces.
Curing, Soaking, & Liming
The skin is preserved using salt or a salt solution to prevent decay, and the sides are folded together before processing. Skin with hair needs to be treated using an oxide solution.
The skin is then soaked to soften it, where it increases by 4-5mm, and then split into two layers:
- Top layer – used for high-quality leather goods, producing full-grain leather.
- Bottom layer – used for lower quality goods, producing split leather or top-grain leather.
Full grain leather has a tighter fiber structure that enhances durability, and it’s more visually appealing.
At Von Baer, we only use full-grain leather in our bags, to ensure you receive the best quality product possible.
Fleshing
This process involves removing any other non-hide tissue from the skin, leaving you with a standardized product.
Tanning
The following stage in leather production is known as tanning, which transforms the skins into leather by preserving them and preventing decomposition.
The process entails placing the skins in a specialized tanning drum, where they are immersed in a tanning solution. The drum is filled with a unique blend of either a vegetable tanning agent or a mixture of chromium salts.
Typically, vegetable tanning agents, which contain tannin extracts naturally present in tree bark, produce a flexible leather that is commonly used in furniture and luggage. On the other hand, chromium salts tend to produce a more elastic leather, making it ideal for products such as handbags and clothing.
Tanning can also be achieved by mixing both chromium and vegetable salts, resulting in a more full-bodied leather characterized by being pliable and soft. Following this step, special fats are then added to the leather during a process known as liquoring, which helps to soften and strengthen it.
The excess moisture must be eliminated next, which is typically done by applying high pressure to the skins via rollers.
After the drying process, the skins are examined and sorted into quality tiers, with those containing flaws being deemed of lower quality. The quality of the leather will determine its intended purpose in the future. Skins treated by using chromium salts will have a pale blue appearance.
Learn more about how the Von Baer tanning process works in this video:
Related articles:
- Suede
- PU leather
- Bonded leather vs Faux leather
- Italian leather
- How to tell if leather is real
- Buffalo leather
- Suede vs Leather
- What is Real Leather
- Pu Leather vs Faux Leather
- Alternative Leather
- Chrome Tan Leather
Re-Tanning
In order to fully prepare the leather for its final use, a second tanning process can take place using either a vegetable mix or chromium salts, and any excess moisture is eliminated using pressure.
After this process is completed, the skins must be dried using methods such as air drying or vacuum drying.
Air drying involves rotating the skin on an overhead conveyor until it is completely dried, while vacuum drying quickly removes all air present around the skin, causing it to shrink slightly and leaving it with a tight and smooth texture. In the re-tanning phase bleaching agent may be used to create an optimal base for the leather dyeing process.
Dyeing
Leather dyeing is a crucial stage in the leather production process, as it gives the final product its desired color. The dyeing process involves the use of highly precise computer programs to create each dye, ensuring a consistent color each time. This color can range from classic black and brown to vibrant hues.
The actual dyeing phase can take a long time, as the skins are placed in large drums with the dye for several hours to ensure the color fully penetrates the skin. After approximately eight hours, a sample is taken to make sure the color is evenly distributed.
The leather is then washed carefully to remove any remaining chemicals or residual dye. Once washed, the skin is dried completely before moving on to the next stage of the leather production process.
Finishing
After dyeing, the final stage in leather production is the finishing process. Here, the leather is manipulated to achieve the desired supple and glossy finish, which not only enhances its appearance but also offers protection and ease of cleaning.
However, if you want naked leather, then this stage is skipped.
A machine is used to lubricate and stretch the fabric with natural oils, tightening the pore structure, resulting in a higher quality finish preferred by consumers. The final step involves applying a finishing spray, which is chosen based on the desired finish.
For example, we can add acrylic for a clean leather finish or mother of pearl for a pearlescent finish, and patterns can be embossed on the leather. In mass production, the leather is hung and moved through a spray line prior to being cured in an oven.
Full-grain leather skips this stage and undergoes an ironing process using varying degrees of heat and pressure to achieve the desired sheen.
The last step in the process is a quality check. This is to make sure that the leather has the right color and is free of defects. Once this is confirmed, the leather is rolled and sent off to be used in the production of leather goods.
Related leather articles:
- Leather
- Faux leather
- Vegan leather
- Bonded vs faux vs real leather
- Bonded leather
- Genuine leather
- Pleather
- Top grain leather
The Science Behind Leather Production
Leather production is a fascinating and complex field of study. Leather is created by tanning animal skins' collagen fibers, which are stretched and treated to produce a flexible and durable material. Different tanning methods each produce distinct leather types.
Each type has its own unique characteristics and qualities. For example, chrome tanning involves treating the skin with chromium salts, resulting in a pliable and soft leather that is easily worked with.
Alternatively, vegetable tanning uses plant extracts for tanning the skin, producing a tougher and more resilient leather that is ideal for heavy-duty applications like belts and boots.
Aside from tanning, leather production involves a range of chemical processes, such as oiling, dyeing, and finishing, that can impact the leather's texture, color, and durability.
Understanding the intricacies of leather production can assist consumers in making informed purchasing decisions while providing valuable information to leather enthusiasts and content creators.
Leather Making Throughout History
People have been using animal skin to make leather for a long time. Common uses in ancient times included clothes, shoes, and even tents.
This was a trial and error process, where they worked out how to prevent the skin from rotting, and used various methods like sun drying, smoking, and other basic chemical experimentation to work out the tanning process.
It became a popular commodity, traded across Europe and the rest of the world.
Related posts:
- Leather guide for beginners
- What is leather patina
- Vegetable tanned leather
- Leather tanning
- What is artificial leather?
- What is full grain leather
- Where does leather come from
- Mushroom leather
- Napa leather
- Pebbled leather
Leather quality and grading
Leather is graded differently by different tanneries, but the broadly agreed standard of measuring leather quality is using the following grades:
- Full-grain leather (best)
- Top-grain leather
- Split-grain leather
- Genuine leather
- Bonded leather (worst)
Genuine and bonded leather are low-quality types of leather.
You can learn more about this in our Leather grades post.
Conclusion
We hope you enjoyed our article on how leather is made.
If you have any questions or comments, contact us at info@vonbaer.com, or leave them in the comments.
Want to read more? Check out our related Leather pages here.

Author: Albert Varkki
Albert Varkki is the co-founder of Von Baer. He understands leather products as a consumer, supplier, and a manufacturer, helping you with the inside knowledge you need, to choose the perfect leather product for you.
We strive for the highest editorial standards, and to only publish accurate information on our website.
Related Articles


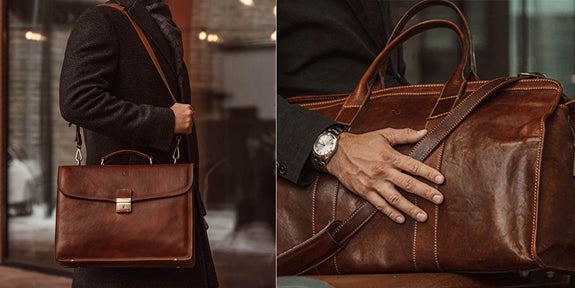

Timeless Leather Bags for Men That Command Authority in 2025
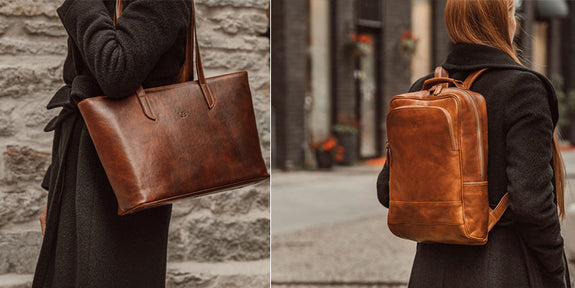

Leave a Comment
Your email address will not be published.